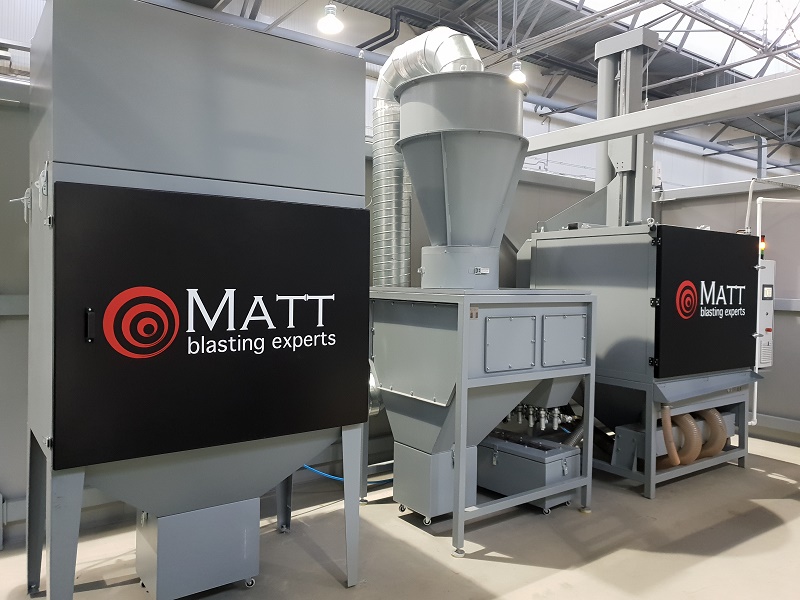
Shot-peening kulowanie czyli sposób na zwiększenie parametrów eksploatacyjnych części
10 maja 2020
Zwiększenie wytrzymałości zmęczeniowej przez shot peening (kulowanie)
Zmęczenie materiału jest zjawiskiem pękania materiału pod wpływem cyklicznie zmieniających się naprężeń znacznie mniejszych niż naprężenia maksymalne dla danego elementu. Czyli może wystąpić wszędzie tam gdzie części poddawane są bardzo częstym obciążeniom o stosunkowo niskiej wartości. Elementy takie to np. korbowody, sprężyny, zęby kół, wały, inne elementy wirujące, wsporniki itp.
W większości przypadków przyczyną mechanizmów zniszczenia zmęczeniowego są naprężenia rozciągające wynikające z zewnętrznych obciążeń lub z naprężeń szczątkowych powstałych podczas wcześniejszych procesów produkcyjnych takich jak: spawanie, szlifowanie lub obróbka skrawaniem. Naprężenia tego typu (rozciągające) podczas pracy elementu sprzyjają powstawaniu i rozprzestrzenianiu się mikropęknięć.
Czym jest kulowanie?
Kulowanie czyli shot-peening, na pierwszy rzut oka jest procesem bardzo zbliżonym do śrutowania. Podczas kulowania powierzchnia obrabiana jest „bombardowana” ziarnami śrutu o kulistym kształcie. Powstałe w ten sposób naprężenia ściskające zapobiegają i opóźniają procesy powstawania mikropęknięć na powierzchni obrobionych elementów. Kulowanie strumieniowe to najbardziej ekonomiczna i praktyczna metoda na wprowadzenie do powierzchni szczątkowych naprężeń ściskających.
Jak działa i co daje kulowanie?
Wszystkie stosowane media używane do procesu kulowania muszą mieć kulisty kształt. Uderzenia kulistych ziaren śrutu powodują małe wgłębienia na powierzchni – zostaje ona „ugnieciona” w wyniku czego powstają naprężenia ściskające. Naprężenia te zapobiegają powstawaniu i propagacji mikropęknięć znakomicie zwiększając wytrzymałość zmęczeniową elementu. Naprężenia te wpływają również na znacznie lepszą wytrzymałość korozyjną w tym zwiększoną odporność na zużycie ścierno-korozyjne (fretting) oraz zużycie wykruszające (pitting). Z naszej oferty do shot peeningu polecamy np. śruty mineralne CeraMATT i GlassMATT, a z mediów metalowych cięty z drutu SteelMATT CW.
Kulowaniu najczęściej poddaje się:
- Sprężyny
- Koła zębate
- Drążki skrętne
- Elementy turbin
- Wały korbowe
- Korbowody
- Wały napędowe
- Wsporniki i konstrukcje
Parametry kulowania
Podczas kulowania najważniejszym aspektem jest powtarzalność procesu, dlatego części muszą być obrabiane w cyklach automatycznych. W odróżnieniu od śrutowania, podczas kulowania nie możemy bezpośrednio, obserwować wyników obróbki (przy śrutowniu wizualnie możemy stwierdzić zmiany powierzchni).
Efekty kulowania mierzymy zatem poprzez pomiar poniższych wartości i utrzymanie stałych parametrów obróbki:
– pomiar intensywności – wielkości wprowadzonych naprężeń
– pomiar pokrycia (stosunek pola powierzchni w którą cząsteczki śrutu uderzyły pola powierzchni całkowitej która miała zostać obróbce).
Do pomiaru intensywności używamy tzw. płytek Almena (Typ A, N oraz C). Płytki Almena, to paski blachy o znormalizowanych wymiarach, grubości i twardości. Płytki te montowane są do wzornika części zostają poddane obróbce kulowaniem z zadanymi parametrami dlatego najważniejszym aspektem podczas obróbki części jest utrzymanie tych samych parametrów obróbki. Parametrami tymi są: rodzaj, twardość i granulacja śrutu, prędkość wylotowa śrutu (ciśnienie robocze lub prędkość turbin), ilość wyrzucanego śrutu, położenie detalu względem dysz lub turbin oraz czas ekspozycji.
W celu zapewnienia skuteczności procesu najważniejszy jest dobór parametrów procesu oraz zapewnienie jego powtarzalności. W tym celu konieczne jest zastosowanie maszyn pracujących w cyklu automatycznym. Firma MATT dostarczyła już dwie takie specjalistyczne instalacje firmie Sulzer Turbo Services – zajmującej się serwisem i regeneracją turbin energetycznych na całym świecie. Najnowsza maszyna, MI150 SP-3, przeznaczona jest do kulowania łopat turbin gazowych. Urządzenie składa się z trzech sekcji komory roboczej, jednostki separacyjnej oraz układu filtracyjnego. 12 pistoletów śrutowniczych umożliwia jednoczesną obróbkę 3 elementów. Kabina posiada pełne sterowanie PLC sprzęgnięte z ekranem operatorskim HMI pozwalającymi na pełną kontrolę nad wszystkimi parametrami oraz zapisanie gotowych programów dla poszczególnych grup części. Dzięki naszej maszynie łopaty turbin pracujące w ekstremalnych warunkach dostają nowe życie.