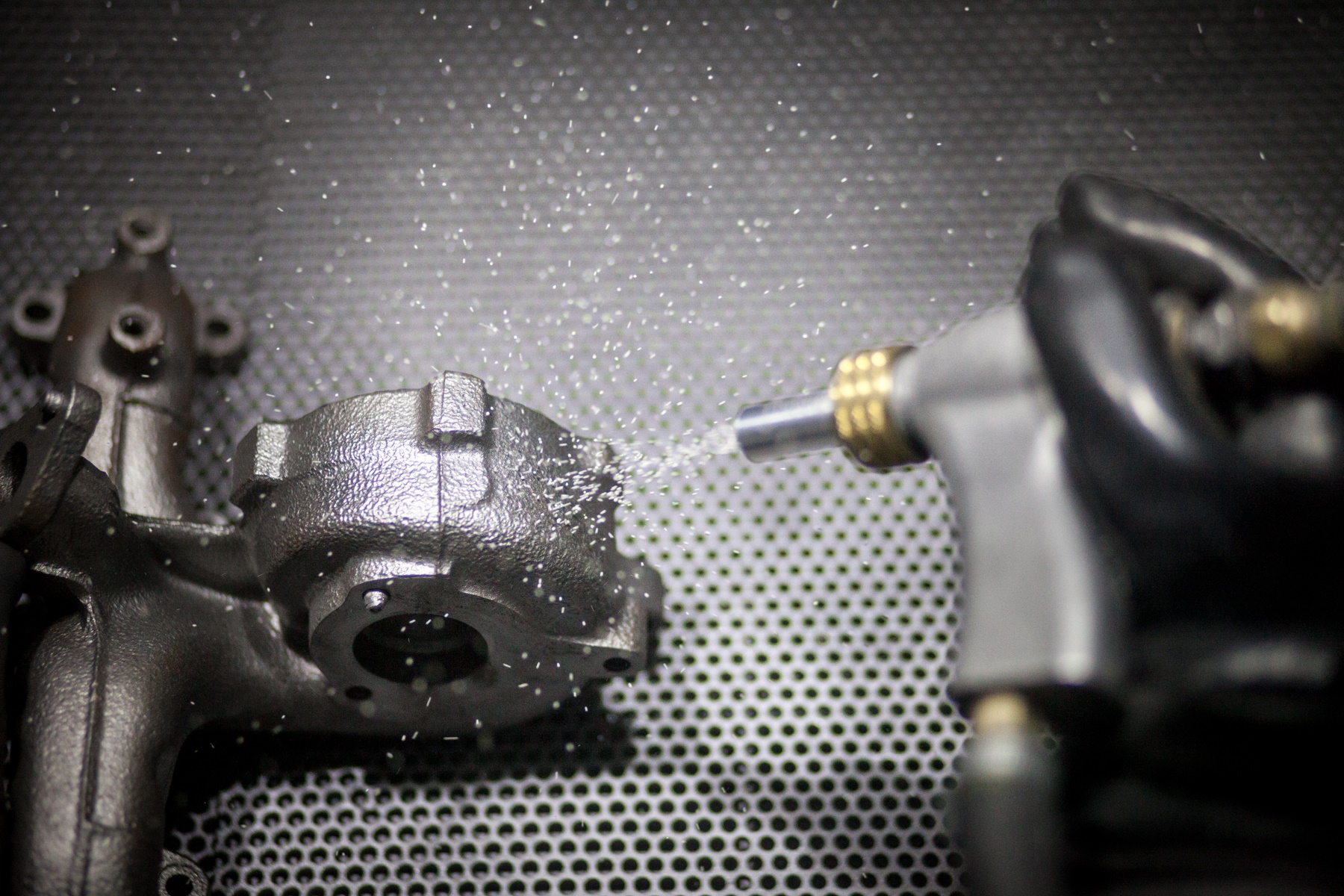
Śrutowanie w regeneracji turbosprężarek
20 stycznia 2020
Chcielibyśmy przybliżyć proces regeneracji części na przykładzie turbosprężarek.
Podczas procesu regeneracji turbosprężarki najlepiej jest oddzielić proces czyszczenia elementów aluminiowych z zimnej części turbosprężarki od elementów żeliwnych z części gorącej.
Rozdzielenie procesu na dwie oddzielne komory śrutownicze pozwala na lepsze dopasowanie parametrów, a co za tym idzie lepszych efektów i wydajności. Nie mniej ważnym aspektem jest bezpieczeństwo. W zmieszanych pyłach stalowym i aluminiowym (np.: w uładzie filtracyjnym) może dojść do samozapłonu pyłu i pożaru. Rozdzielenie procesu zapobiega również wbijaniu pyłów zawierających żelazo w powierzchnię aluminiową, co może powodować szybkie powstawanie rdzawego nalotu na powierzchniach aluminiowych.
Części aluminiowe
Te najlepiej jest obrabiać za pomocą mikrokulek szklanych o różnych granulacjach w zależności od tego jaką chropowatość chcemy uzyskać. Mikrokulki szklane zapewniają estetyczną powierzchnie o bardzo jasnej, naturalnej dla aluminium barwie. Dodatkowo, niska gęstość szkła w porównaniu do pozostałych mediów pozwala uzyskać wysoką efektywność czyszczenia przy użyciu niedrogich i prostych w budowie kabin inżektorowych. Kabiną stworzoną z myślą o takich zastosowaniach jest Cabimatt MG100 o przestrzeni roboczej 1000x600x600mm.
Do elementów bardzo drobnych i delikatnych doskonałym rozwiązaniem jest kabina MG-T 100 wyposażona w kosz obrotowy, może ona pracować w trybie automatycznym.
Jeśli potrzebna jest wyższa wydajności obróbki, konieczne jest zastosowanie automatycznych śrutownic wirnikowych, w których śrut wprawiany jest w ruch za pomocą siły odśrodkowej i łopatek turbiny, a nie sprężonego powietrza jak ma to miejsce w przypadku maszyn pneumatycznych. W maszynach wirnikowych nie ma możliwości zastosowania szkła jako medium śrutowniczego. Rozwiązaniem są śruty nierdzewne, staliwne lane lub stalowe cięte z drutu.
W zależności od typu i wielkości elementów można zastosować maszyny:
Turbomatt TG typu muldowe, z taśmą gumową – do mniejszych elementów, które podczas ruchu na taśmie nie będą się o siebie kaleczyły.
Turbomatt HV typu zawieszkowego (link) do elementów większych, które łatwiej mogą ulec uszkodzeniu.
Turbomatt TS typu stołowego do dużych i ciężkich elementów.
Elementy staliwne lub żeliwne przeznaczone do regeneracji, wskutek warunków eksploatacji czyli: dużej zmiany temperatur, wilgoci i obecności soli, często pokryte są grubą warstwą korozji lub wymagają usunięcia starych powłok ochronnych. Wymaga to zastosowania innych środków technologicznych i parametrów procesów.
Części stalowe i żeliwne
Do efektywnego usunięcia korozji, najlepiej zdają egzamin śruty staliwne. Ich ciężar i duża energia uderzenia bardzo szybko i efektywnie oczyszczają powierzchnie tam gdzie mikrokulki szklane działają zbyt delikatnie. Do utrzymania wysokiej wydajności w przypadku ciężkich mediów konieczne jest użycie kabin ciśnieniowych w których śrut jest „wypychany” ze zbiornika będącego pod ciśnieniem. Jeśli wymagana jest wyższa wydajność możliwe jest zastosowanie, tak jak w przypadku części aluminiowych, śrutownic wirnikowych zawieszkowych lub muldowych. W przypadku śrutownic muldowych istnieje znacznie mniejsze ryzyko kaleczenia powierzchni detali o siebie niż w przypadku miękkiego aluminium. Do części stalowych i żeliwnych nie ma potrzeby stosowania śrutów nierdzewnych. Doskonale sprawdzą się śruty staliwne wysokowęglowe. Dostępne w naszej ofercie śruty Steelmatt S charakteryzują się bezkonkurencyjnym stosunkiem żywotności do ceny oraz pozwalają uzyskać estetyczną, gładką i czystą powierzchnię obrobioną.
Jeśli jesteście Państwo zainteresowani doborem maszyn mediów lub parametrów procesu zapraszamy do przeprowadzenia prób w naszej pracowni.